Processes and Capabilities
Taylor Foundry
Our primary cast iron manufacturing facility is in Wichita Falls,Texas. We have been pouring iron at the same location since 1925. Taylor operates a cupola furnace using maximum achievable control technology (MACT). Green sand horizontal molding is achieved with auto-cycle cope and drag molding machines utlizing low frequency, long stroke anvil jolt for pre-compaction and simultaneous jolt squeeze for final compaction.
- 2 sand mixing mullers
- 4 molding lines with 4 pouring bays
- Castings from 1 pound to 2,000 pounds.
- 2 shot blast machines and 4 grinding lines
- Paint and coatings by dip station or spray booth.
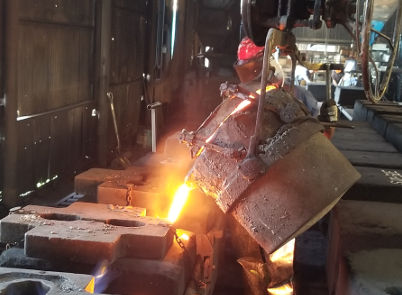
Experience produces quality. Many on our staff measure their employment with us in decades. Our foundry manager has been with us for more than 20 years. Our melt supervisor - more than 40 years. We have sales team members that have been with us more than 20 years.
We melt gray iron scrap consisting of #1 cupola cast scrap sourced from a variety of long term vendors who are familiar with our requirements. All scrap loads are inspected, sub standard loads are rejected. During melting, temperatures are constantly monitored at the transfer ladle and pouring ladles.
Product conformity is verified with instruments and gauges.
- Value added services include:
- Product Design / Weldment Conversions
- Machining and Fabricating
- Assembly
- Painting / Coatings
- Hardware Design and Procurement
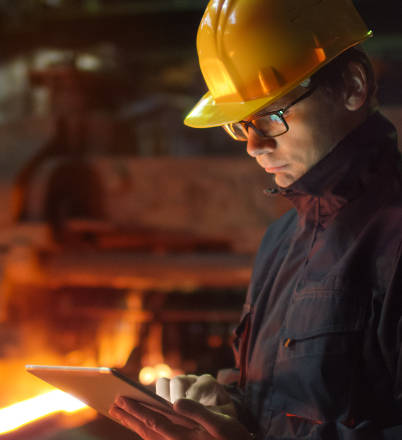
Alliance Foundries
In early 2018 we purchased a cast iron importer and distribution firm. The resulting integration provided us with an alliance of overseas iron foundries which expanded our capabilities and capacity.
Through these alliances, we are able to offer our customers the widest variety of processes available.
- Gray Iron, Ductile Iron, Austempered Ductile Iron, Compacted Graphite Iron
- Ore and Scrap Melting
- Cupola Melting - Electric Melting
- Dry Sand Casting - Resin Sand Casting - Green Sand Casting
- Floor Molding - Disa Arpa Molding - BMM BT/CT molding
- V Process - Vacuum Molding
- Sinto Flaskless High Pressure Molding
- Dip Painting - Spray Painting - Powder Coating
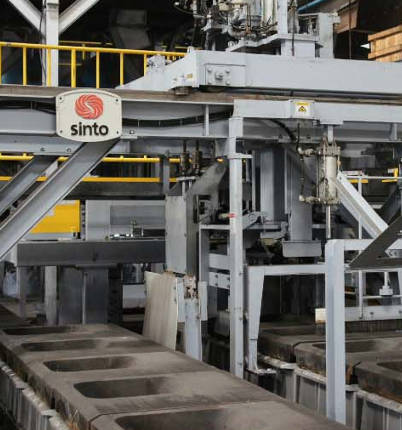
Supply Chain
We have vast experience as suppliers for Original Equipment Manufacturers and understand the requirements they have for their vendors. In addition to manufacturing high quality iron castings, we can provide logistical expertise to include import/export shipments, freight options, and multiple destination distribution.
Our primary facility has its own rail spur and is located on an interstate highway. Additionally, we have warehouse space available for safety stock.
Give us a call to learn more about what we can do for you.
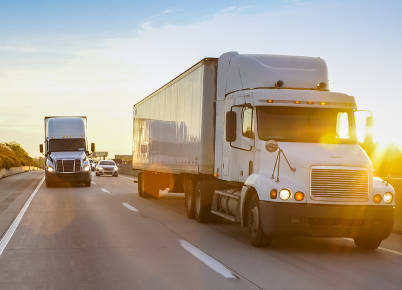
Foundry Basics
Considering the knowledge and skill required to operate a cast iron foundry, most operators could, given the required time and investment, produce almost any cast iron part. The reality is that most foundries specialize in only a few product lines and processes. By specializing, they keep their production time and costs as low as possible and their quality as high as possible. Taylor Foundry Company, together with our own green sand foundry and global alliances, is able to provide the widest variety of products and cast iron manufacturing processes available.
SAND
The sand that is typically used to create casting molds is a silica sand (SiO2) mixed with various binders to maintain the shape of the mold. Sand is resistant to high temperatures allowing many different metals to be cast. Sand grains are very important and are specified by their size and shape.
Green Sand Molding
Uses a mixture of sand, water and a clay or binder.
Green Sand Molds are the least expensive and most widely used in the metal casting industry.
Skin Dried Molding
Starts much like a green sand mold but with additional binding materials.
The cavity surface is dried with a torch or other heating equipment to increase mold strength.
This improves the dimensional accuracy and surface finish but increases the chance of collapse.
Dry Skin Casting takes more time, decreasing production rates.
Dry Sand Molding
In a dry sand mold the sand can be green sand modified with additional binders or often sand mixed only with organic binders.
The mold is then strengthened by baking in an oven.
This type of mold has high dimensional accuracy but results in lower production rates.
No Bake Molding
The sand in a no bake mold is mixed with liquid resin.
The mold, due to the addition of the resin, will harden at room temperature.
Produces excellent surface finishes and can be used for very large castings.
The Cold Setting Process refers to any of several systems for binding molds or cores which relies on the use of catalysts rather than heat to harden.
The cold box process usually refers to a rapid core making process.
Hardening is achieved by chemical reaction rather than conventional baking.
A resin is added to the sand which reacts chemically when exposed to an accelerator, usually an organic gas, and hardens very quickly.
This reaction occurs at room temperature.
MOLD PACKING
There are many ways to pack the sand around a pattern, inside a flask, to create the mold cavity. Different methods will affect the dimensional accuracy as well as the surface finish. The sand can be packed by hand or with hand held pneumatic devices. A sand slinger fills the flask by propelling the sand at high pressure. A jolt/squeeze machine rapidly jolts the flask to distribute the sand and then uses pneumatic or hydraulic pressure to compress it. Vacuum molding packs the sand by removing the air between the flask and a thin sheet of plastic that covers the pattern.
Automated Flask-less Molding - In conventional molding a tight flask or pop-off flask is used for each individual mold produced. In Automated Flask-less Molding, a master flask is integrated into the mold producing unit with sand blown against the pattern inside. Once the mold is stripped from the mold producing unit, the two halves are held together with enough pressure to allow the pouring of the metal.